7.3.1 Laminaatin rakenne
Laminaatin rakenteen selvittäminen on usein toistuva tehtävä sekä kehitystyössä että laadunvarmistuksessa. Määritettäviä ominaisuuksia ovat tavallisimmin lujitepitoisuus, lujiterakenne ja laminaatin huokoisuus.
Lujitepitoisuutta voidaan karkeasti arvioida mittaamalla laminaatin paksuus. Kun laminaattiin käytettyjen lujitekerrosten lukumäärä ja neliömassa sekä lujitteen tiheys ovat tunnetut, lujitepitoisuus voidaan edelleen laskea kaavalla (6.7). Tarkempaan tulokseen päästään punnitsemalla näytepala, poistamalla siitä matriisimuovi ja punnitsemalla jäljelle jäävä lujite. Lujitteesta ja matriisimuovista riippuen matriisimuovi poistetaan polttamalla tai liuottamalla. Laminaattinäytteestä jäävästä lujitepakasta voidaan lisäksi selvittää lujiterakenne eli lujitekerrosten määrä, suuntaukset ja pinoamisjärjestys.
Laminaatin huokoisuus voidaan määrittää punnitsemalla näytepala ilmassa ja vedessä. Tuloksista saadaan laskettua komposiitin tiheys. Huokoisuus saadaan laskettua kaavalla (6.9), kun aineosien tiheydet ja massaosuudet tunnetaan. Huokoisuus voidaan myös määrittää näytepalasta mikroskoopin avulla. Tapa on edellistä suositeltavampi, sillä se antaa kuvan myös huokosten koosta, kokojakautumasta ja sijainnista. Koko tuotteen huokoisuutta menetelmällä ei saada selville, ellei näytepaloja oteta riittävän monesta kohdasta.
Lujitepitoisuutta voidaan myös tutkia termogravimetrisella analyysillä eli TGA-laitteistolla, joka mittaa näytteen painon muutosta, kun sitä kuumennetaan vakionopeudella. Kuumennusnopeus on tavallisesti kymmeniä asteita minuutissa (20…40 °C/min), joten mittaus on nopea suorittaa. Analyysillä saadaan määritettyä myös lisä- ja täyteainepitoisuudet edellyttäen, että aineosat hajoavat termisesti eri lämpötiloissa. Mittaustulos ilmaisee lisäksi laminaattiin imeytyneen kosteuden määrän.
7.3.2 Valmistuksen aikaiset muodonmuutokset
Laminaatin
valmistuksen aikainen lineaarikutistuma saadaan määritettyä vertaamalla
näytepalan mitta-alueen pituutta muotin vastaavaan pituuteen. Mittaustulosten
käsittelyssä on otettava huomioon lämpötilamuutosten aiheuttamat muotin
mittamuutokset. Nurkkien kulmamuutoksia voidaan mitata valmistamalla edustavia,
esimerkiksi U-profiilin muotoisia näytepaloja.
7.3.3 Laminaatin kovettumisaste ja kovuus
Kertamuovipohjaisen laminaatin kovettumisaste voidaan määrittää pyyhkäisykalorimetrilla (Differential Scanning Calorimeter, DSC). Laite mittaa näytepalan sitoman/luovuttaman energian määrää näytteen lämpötilaa nostettaessa. Mikäli näytepala on osittain kovettumaton, kovettumisreaktio menee loppuun mittauksen aikana. Eksotermireaktiossa vapautuu energiaa, jonka määrästä voidaan määrittää näytteen kovettumisaste.
DSC-mittauksen ongelmana on laitteiston kalleus. Käytännön työssä kovettumisaste määritetäänkin usein likimääräisemmin mittaamalla kovetetun hartsivaloksen tai laminaatin kovuutta. Mitattava suure on Barcol-kovuus, jonka arvo ilmaistaan asteikolla 0…100. Kovuus mitataan laitteella, joka iskee teräksisen neulan jousivoimalla näytteen pintaan. Kovuusarvo on verrannollinen neulan tunkeutumaan. Kovuusarvoon vaikuttaa matriisin kovettumisasteen ohella näytteen rakenne. Esimerkiksi kovettuneen laikuitulujitetun polyesterilaminaatin Barcol-kovuus on tyypillisesti 40…45, kun samasta hartsista valmistetun valoksen vastaava arvo on 35…40.
Kestomuovien kovuutta mitataan tavallisesti Rockwell-kovuudella. Kovuus määritetään laitteella, joka mittaa teräksisen kärjen tai timanttikärjen tunkeutumaa näytteeseen, kun kärkeä painava voima kasvaa määritellystä minimiarvosta määriteltyyn maksimiarvoon. Rockwell-kovuutta mitataan eri asteikoilla, jotka perustuvat erilaisiin mittauskärkiin. Kestomuoveilla yleisiä asteikkoja/kärkiä ovat L, M ja R, joista L soveltuu pehmeille ja R koville muoveille. Kestomuovien tyypilliset kovuusarvot ovat HRM 49…102 ja HRR 80…124 koodien viimeisen kirjaimen ilmoittaessa käytetyn kovuusasteikon.
Hyvin elastisten materiaalien, esimerkiksi kumien kovuutta mitataan Shore-kovuudella. Kovuusarvon määrittää jousikuormitetun kärjen painuma näytteeseen. Kovuusarvot ovat tyypillisesti välillä Shore D 54…80
7.3.4 Hygrotermiset ominaisuudet
Lämmönkestävyys
Tärkeimmät matriisimuovien ja laminaattien lämmönkestävyyttä mittaavat koestusmenetelmät ovat lasittumislämpötilan Tg ja taipumislämpötilan eli HDT-arvon määritys.
Lasittumislämpötila määritetään näytepalasta pyyhkäisykalorimetrilla eli DSC-laitteella. Lämpötila näkyy DSC-termogrammissa kulmakertoimen muutoksena. Mikäli näyte on osittain kovettumaton, termogrammissa huippuna näkyvä jäännösreaktiivisuus saattaa peittää muutoskohdan. Tässä tapauksessa (täysin kovettuneen muovin) Tg saadaan määritettyä toistamalla mittaus ensimmäisen ajon aikana kovettuneella näytteellä.
Lasittumislämpötilaa voidaan mitata myös termomekaanisella laitteistolla (Thermo Mechanic Analysis, TMA), jossa näytettä koskettava mittapää mittaa näytteen paksuuden muutosta lämpötilan noustessa asetetulla nopeudella. Menetelmä pohjautuu muovin lämpölaajenemiskertoimen voimakkaaseen muutokseen lasittumislämpötilassa.
Taipumislämpötila mitataan kohdistamalla tasaleveään, suorakaiteen muotoiseen koesauvaan vakiona pidettävä taivutuskuorma. Kuormitetun sauvan lämpötilaa nostetaan tasaisella nopeudella, kunnes sauvan taipuma HDT-lämpötilassa on kasvanut standardissa määrättyyn arvoon.
Lämpölaajenemiskerroin
Lämpölaajenemiskerroin määritetään mittaamalla koekappaleen pituuden muutosta sitä lämmitettäessä. Lämpölaajenemiskerroin voi olla lämpötilan funktio, joten mittaus on tehtävä tarpeellisen laajalla lämpötila-alueella. Kuvassa 7.2 on esitetty lämpölaajenemisen mittaustulokset hiilikuitu/epoksi-yhdensuuntaislaminaatille kuituja vastaan kohtisuorassa suunnassa. Lämpölaajenemiskertoimen arvon nähdään olevan likimain vakio lasittumislämpötilaan 170 °C asti. Lämpölaajenemiskerroin voidaan myös määrittää näytepalasta TMA-laitteistolla.

Kuva 7.2 Hiilikuitu/epoksi-yhdensuuntaislaminaatin lämpölaajeneminen poikittaissuunnassa. [1]
Kosteusabsorptio
Kosteusabsorptiota mitataan altistamalla näytepala haluttuun ympäristöön ja punnitsemalla se määräajoin. Altistus tehdään sääkaapissa tai vedessä. Mittaustuloksena saadaan kosteuspitoisuus ajan funktiona. Esimerkkinä on kuvassa 7.3 erään matriisiepoksin kosteusabsorptio 70 °C:ssa vedessä. Mittauksiin voidaan sisällyttää näytekappaleen mitta-alueen pituuden määritys. Tuloksista saadaan edelleen laskettua kosteuslaajenemiskerroin.
Koejärjestelyistä on huomattava, että koekappaleen pinta vaikuttaa merkittävästi kosteusabsorptioon. Laminaattien kosteusabsorptioon vaikuttaa myös se, pääseekö kosteus tunkeutumaan laminaattiin reunojen kautta vai ovatko laminaatin reunat tiivistetyt. Tavallisesti reunat tiivistetään, koska laminaattirakenteet ovat käytännössä suuria levymäisiä kappaleita, joihin kosteus imeytyy reuna-alueita lukuun ottamatta vain paksuussuunnassa.
Kappaleen 7.3.1 mukaisesti laminaatin tai valoksen kosteuspitoisuutta voidaan myös mitata näytepalasta TGA-laitteistolla.
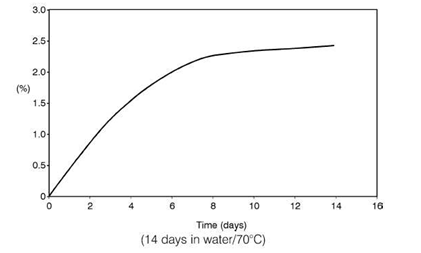
Kuva 7.3 Erään matriisiepoksin kosteusabsorptio 70 °C:ssa vedessä. [1]
7.3.5 Mekaaniset lyhytaikaisominaisuudet
Mekaanisia lyhytaikaisominaisuuksia joudutaan määrittämään kokeellisesti kerroksille ja laminaateille. Kerroskokeet tehdään käytännössä useasta samansuuntaisesta kerroksesta muodostetulle laminaatille. Kerroskokeiden tarkoituksena on usein suunnitteluarvojen määrittäminen. Laminaattikokeilla tyypillisesti varmennetaan laskennallisesti määritettyjen jäykkyys- ja lujuusarvojen oikeellisuus. Kun koestuslämpötila on normaalista poikkeava, kokeet tehdään ympäristökammiolla varustetulla aineenkoestuslaitteella. Koekappaleiden mahdollinen kosteusaltistus tehdään sääkaapissa.
Vetokokeet
Vetokokeen tavoitteena on tavallisesti kerroksen tai laminaatin kimmomodulin, vetolujuuden ja murtovenymän määrittäminen. Kokeissa mitataan usein myös vetokuormituksen aiheuttamaa poikittaista suppeumaa kuvaavan Poissonin vakion arvo. Lisäksi voidaan mitata kuormituksen aiheuttamaa koekappaleen säröilyä. Helposti suoritettavina vetokokeet soveltuvat hyvin materiaaliominaisuuksien määrityksen ohella tuotannon laadunvarmistusmenetelmäksi.
Laminaattien vetokoestandardit pohjautuvat lujittamattomille muoveille kehitettyihin koemenetelmiin. Koekappale on tutkittavasta materiaaliyhdistelmästä riippuen tasaleveä tai keskeltä kavennettu sauva (kuva 7.4). Koesauvan muodolla pyritään saamaan sauvan pettämiskohta kiinnityshäiriöistä vapaalle keskialueelle. Kavennettu sauva sopii hyvin koekappaleeksi, kun tutkittavana on alhaisen jäykkyyden omaava laminaatti, vähän suunnattu laminaatti tai ±45° -ristikkäislaminaatti. Tasaleveä sauva on yleensä parempi tutkittaessa lujuusominaisuuksiltaan voimakkaasti suunnattuja laminaatteja. Koesauvan päihin liimataan usein alumiini- tai laminaattilevyt kiinnityskohdan vahvistamiseksi ja aineenkoestuslaitteen tarraimien tarttuvuuden parantamiseksi.
Koetta suoritettaessa koesauva asennetaan aineenkoestuslaitteeseen tarkasti vetokuormituksen suuntaisesti. Pienetkin asennusvirheet vaikuttavat mittaustuloksiin erityisesti, kun tutkittavana on lujuusominaisuuksiltaan voimakkaasti suunnattu materiaaliyhdistelmä. Kuormitusnopeus määritellään tavallisesti liikkuvan kiinnitysleuan nopeutena. Kuormitusnopeudet vaihtelevat standardista riippuen välillä 2…10 mm/min.
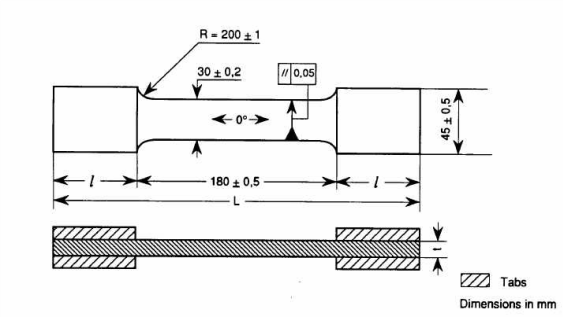
Kuva 7.4 Keskeltä kavennettu vetokoesauva.
Mitattavia suureita ovat yleensä aina koesauvaan kohdistettu kuorma Fx ja sitä vastaava sauvan mitta-alueen venymä ex. Venymää mitataan ekstensiometrillä tai venymäliuskalla. Kun mitta-alueen poikkipinta-ala A tunnetaan, voidaan edelleen laskea kuormaa vastaava sauvan normalisoitu vetojännitys:
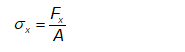
(7.1)
Jännitys/venymä-arvopareista muodostuu laminaatin jännitysvenymäkuvaaja. Sen lineaariselta alueelta valitaan kaksi jännitys/venymä-arvoparia, joista saadaan määritettyä laminaatin kimmomoduli:
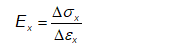
(7.2)
Kun kokeessa lisäksi mitataan koesauvan poikittaista venymää ey, saadaan ex ey – kuvaajan lineaariselta alueelta valituista venymäpareista laskettua Poissonin vakio:
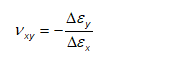
(7.3)
Puristuskokeet
Puristuskokeiden tavoitteet ovat vastaavanlaiset kuin vetokokeiden. Kokeilla mitataan tavallisesti laminaatin kimmomodulia, puristuslujuutta ja murtovenymää, toisinaan myös Poissonin vakiota ja jännitystä, jolla laminaatti alkaa säröillä.
Puhtaan puristuskuormituksen aikaansaaminen koekappaleeseen on varsin hankalaa. Puristuskoetta vaikeuttaa lisäksi se, että ohuet koesauvat nurjahtavat jo pienillä kuormituksilla. Kokeissa tarvitaankin kuormitusjigiä, jossa koekappaleeseen kohdistetaan puristuskuormitus niin, että sauvan nurjahdus on estetty.
Standardoituja muovikomposiittien puristuskokeita on useita. Koesauvat ovat tyypillisesti lyhyitä, standardista riippuen kavennettuja tai kaventamattomia. Sauvaa kuormitetaan joko suoraan sauvan päistä tai siirtämällä puristuskuorma sauvan vahvistettuun päähän tarraimilla. Kuvan 7.5 koesauvassa mitta-alue on niin lyhyt, että laminaatin puristuslujuus saavutetaan ennen sauvan nurjahtamista. Sauva kuormitetaan kuvan mukaisesti jigissä, jonka rakennetta selvittää kuva 7.6. Puristuskokeiden tuloksia käsitellään samaan tapaan kuin vetokokeiden tuloksia.

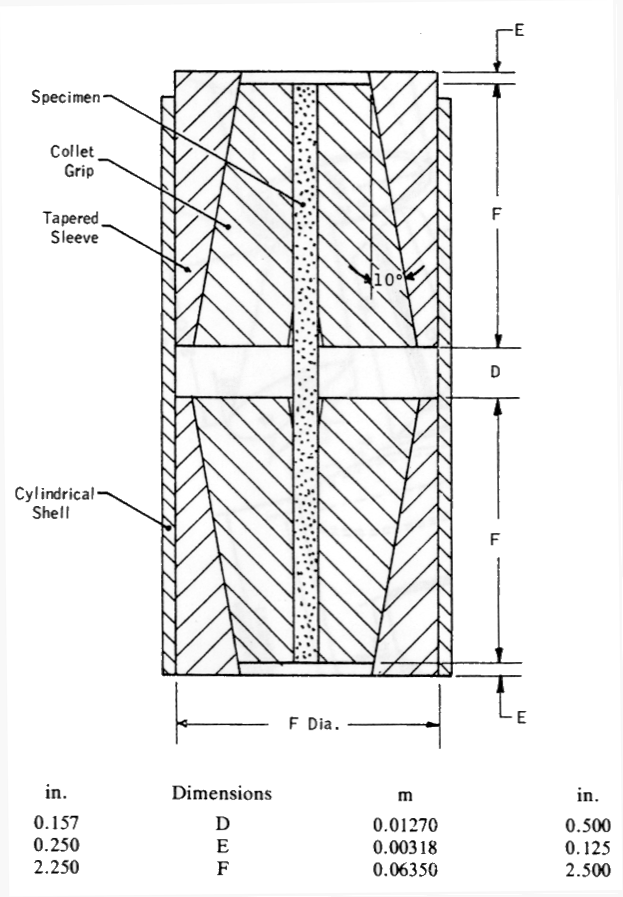
Kuva 7.5 Puristuskoesauva ja sauvan kuormitusjigi (esimerkki).
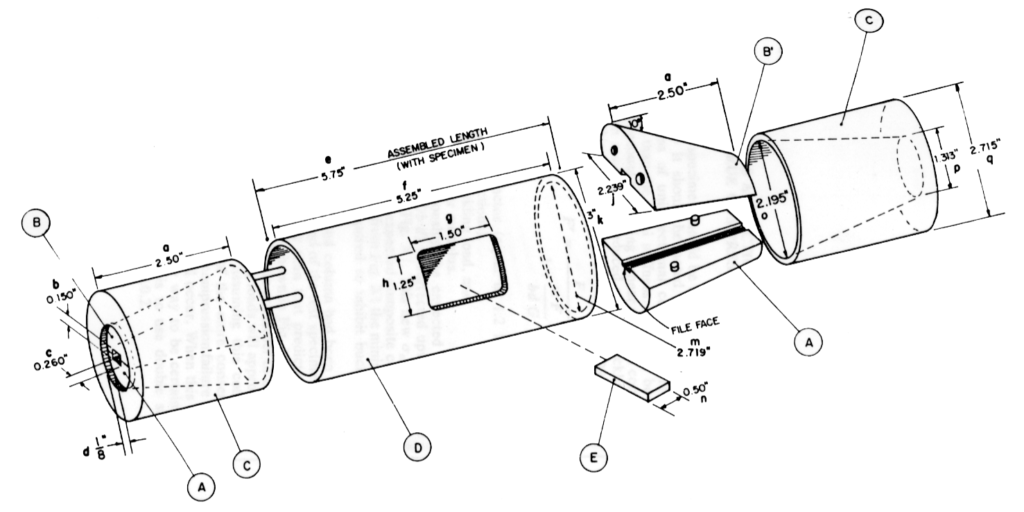
Kuva 7.6 Puristuskuormitusjigin rakenne.
Puristuskokeessa mitattu laminaatin moduli voi jossain määrin erota vetokokeessa mitatusta modulista, koska modulin arvoon vaikuttaa myös laminaatin rakenne, esim. kuitujen mutkaisuus. Puristuslujuus voi materiaaliyhdistelmästä ja kuormitussuunnasta riippuen selvästi erota vetolujuudesta. Tyypillisesti laminaattien puristuslujuudet ovat melko selvästi vetolujuuksia alhaisemmat.
Leikkaus laminaattitasossa
Laminaattitason leikkauskokeilla haetaan lujuuslaskelmien pohjaksi kerroksen vastetta leikkauskuormitukseen tai varmistetaan laminaattiteorian antamia tuloksia suunnitellulle laminaattirakenteelle. Haettavia teknisiä suureita ovat liukumoduli, leikkauslujuus, murtoliukuma sekä mahdollisesti myös säröilyn alkua vastaava jännitys.
Puhtaan, kontrolloidun leikkausrasituksen kohdistaminen tasolevyyn on käytännössä hankalaa. Leikkauskokeita onkin vuosien mittaan kehitetty lukuisia, joista vain osa on standardoitu. Eräs yksinkertaisimmista ja edelleen parhaista menetelmistä ortotrooppisen kerroksen leikkausominaisuuksien määritykseen on symmetrisen, ±45°-laminaatin vetokoe. Kokeessa mitataan laminaatin jännitysvenymäkuvaaja ja Poissonin vakio, joiden perusteella voidaan arvioida kerroksen leikkausjäykkyys ja -lujuus luvussa 8 esitetyin laskennallisin menetelmin. Kerrosominaisuuksia mitataan myös vetokokeella, jossa kerroksen pääsuunta poikkeaa 10° kuorman suunnasta.
Toinen tunnettu leikkausominaisuuksien määrityskoe on ohutseinäisen putken vääntö. Kun putki pääsee vapaasti muotoutumaan aksiaalisuunnassa, seinämään kohdistuu puhdas leikkausrasitus, joka saadaan lausekkeesta:
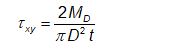
(7.4)
missä MD on vääntömomentti, D on putken keskihalkaisija ja t on putken seinämäpaksuus. Jännitysvenymäkuvaajan määritykseen tarvitaan lisäksi putken seinämän liukuma, joka voidaan määrittää putken vääntymästä tai venymäliuskoilla suoraan putken seinämästä. Vääntökokeen haittapuolena on koekappaleiden vaikea valmistettavuus. Koekappaleiden valmistus tasomaisten kappaleiden valmistusta vastaavasti voi myös olla mahdotonta, jolloin valmistustekniikan vaikutus ominaisuuksiin jää selvittämättä.
Tasoleikkausominaisuudet voidaan määrittää myös ns. rail-shear-kokeella, jossa koekappaleena on laminaattilevy. Levyyn kiinnitetään kiskot, jotka edelleen kiinnitetään aineenkoestuskoneeseen niin, että kuormituksessa kahden kiskon väliseen levykenttään kohdistuu leikkausrasitus. Menetelmästä on kaksi variaatiota, joista toisessa kiskoja on kaksi, toisessa kolme (kuva 7.7). Levykenttään kohdistuva leikkausjännitys saadaan jakamalla siihen kohdistuva leikkausvoima Qxy levyn paksuudella ja levykentän korkeudella
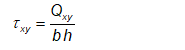
(7.5)
Rail-shear-menetelmät ovat toimivia, mutta hankalakäyttöisiä koekappaleiden suuren koon ja vaikean asennuksen takia.
Viime aikoina yleistynyt leikkauskoe on ns. Iosipescu-koe, jossa koekappale on kuvan 7.8a mukainen lovettu sauva. Sauvaa kuormitetaan erityisessä jigissä kuvan 7.8b mukaisesti niin, että leikkausvoima on vakio loven alueella ja taivutusmomentti nolla loven pohjan määrittelemässä poikkileikkauksessa. Kuormitusta F vastaava leikkausjännitys on
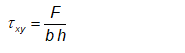
(7.6)
missä b on koesauvan leveys ja h loven pohjan määrittelemän poikkileikkauksen korkeus. Kun kuormituksen ohella mitataan laminaatin liukumaa loven pohjan määrittelemässä poikkileikkauksessa, saadaan määritettyä laminaatin leikkausjännitys/liukuma-kuvaaja. Iosipescu-menetelmän hankaluutena on tarvittavan kuormitusjigin ohella se, että sauvan häiriötön mitta-alue on varsin pieni. Kuormitusjigi on kaaviomaisesti esitetty kuvassa 7.9.
Laminaateille kehitettyjen tasoleikkauskokeiden hyvyyttä on arvioitu taulukossa 7.1. Taulukossa arvioitujen ominaisuuksien, niiden painotusten ja menetelmien pisteytysten pohjalta parhaita menetelmiä ovat ±45°-laminaatin vetokoe ja Iosipescu-koe. Painotukset ja pisteytykset ovat kuitenkin subjektiivisia, joten taulukon lopputulos menetelmien hyvyydestä on vain suuntaa antava.
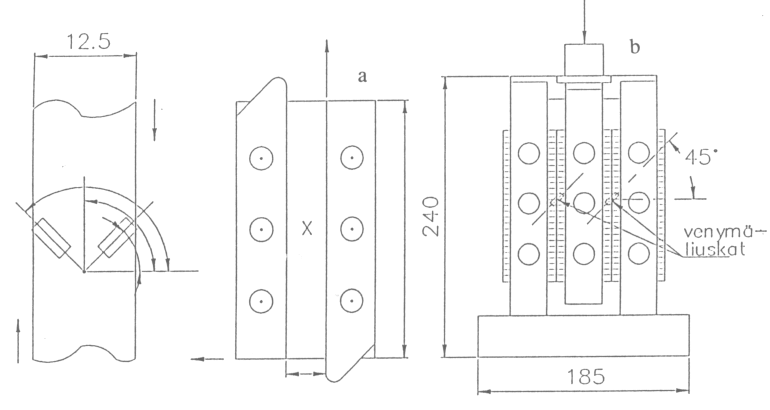
Kuva 7.7 Rail-shear leikkauskokeet.

Kuva 7.8 Iosipescu-leikkauskoesauva ja sen kuormitustapa

Kuva 7.9 Iosipescu leikkauskokeessa käytetty kuormitusjigi.
Taulukko 7.1 Laminaatin tasoleikkausominaisuuksien määrittämiseen käytettyjen menetelmien vertailu.
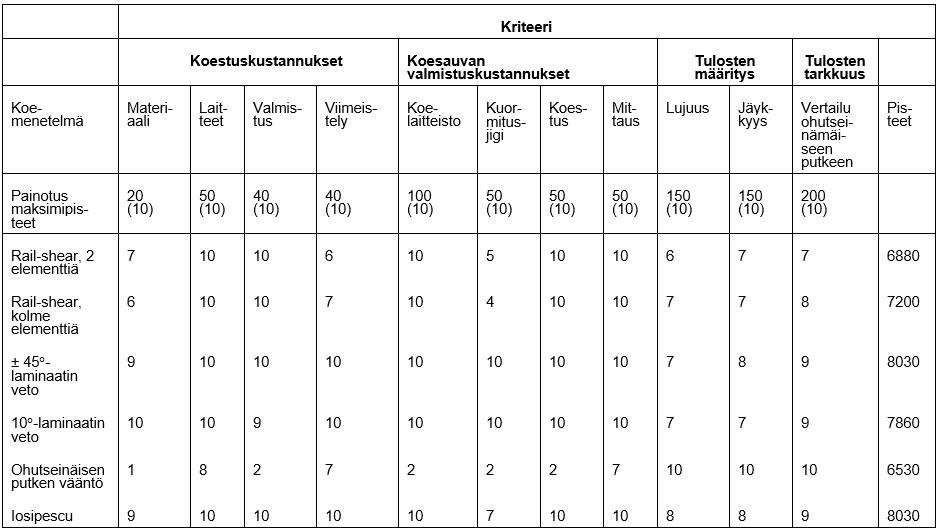
Taivutuskokeet
Taivutuskokeen järjestelyt ovat kuvan 7.10 mukaiset. Koesauva on tasaleveä ja asetettu rullamaisten tukien päälle. Sauvaa kuormitetaan joko yhdellä tai kahdella pyöreällä kuormituspäällä. Edellisessä tapauksessa koetta nimitetään kolmipistetaivutukseksi, jälkimmäisessä tapauksessa nelipistetaivutukseksi.
Kuorman vaikutuksesta koesauvan poikkileikkauksia rasittavat kuvan 7.10 mukaiset taivutusmomentit ja leikkausvoimat. Taivutusmomentti aiheuttaa alapintaan vetojännitystä ja yläpintaan puristusjännitystä. Koesauvan mitat ja tukiväli valitaan niin, että taivutusmomentti on sauvan kuormankantokyvyn kannalta kriittinen kuormituskomponentti. Sauvan paksuuden ja tukivälin suhde on kuitenkin valittava niin suureksi, että taivutusmomentin aiheuttama taipuma on riittävällä tarkkuudella teknisen taivutusteorian mukainen pettämishetkeen asti.
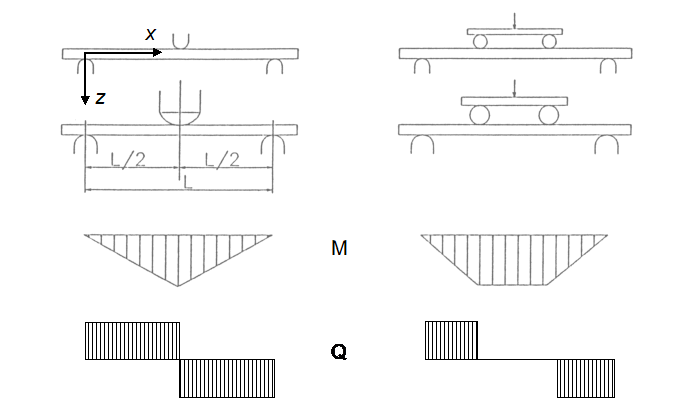
Kuva 7.10 Kolmi- ja nelipistetaivutus, koejärjestely ja kuorman koesauvaan aiheuttamat taivutusmomentit ja leikkausvoimat.
Kolmipistetaivutuksessa suurin taivutusrasitus kohdistuu koesauvan keskelle (kuva 7.10). Kuormituspää aiheuttaa samaan kohtaan paikallisia rasituksia, mistä syystä sauva yleensä pettää ennen kuin yläpinnan todellinen puristuslujuus on saavutettu. Nelipistetaivutuksessa taivutusmomentti on vakio ja leikkausvoima nolla kuormituspäiden välisellä alueella. Menetelmä onkin jossain määrin kolmipistetaivutusta parempi, vaikka pettäminen edelleen tapahtuu pääsääntöisesti kuormituspään kohdalla. Käytännössä paikallisia rasituksia tasataan usein kuormituspäiden ja koesauvan väliin asennettavilla kumilevyillä.
Taivutuskokeessa sauvan kuormaa kasvatetaan tasaisella nopeudella. Kuormitusnopeus valitaan niin, että sauvan pintavenymä kasvaa likimain nopeudella de/dt = 0,01 1/min. Tätä vastaava kuormituspään liikenopeus v saadaan kumpaakin kuormitustapaa vastaten lausekkeesta:
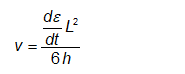
(7.7)
missä L on tukiväli ja h koesauvan paksuus.
Kokeessa mitataan kuorman ohella taipumaa sauvan keskellä, toisinaan myös pintojen venymiä. Vastaavasti kuin veto- ja puristuskokeessa voidaan lisäksi mitata, millä kuormituksella laminaattiin alkaa muodostua säröjä. Sauvan petettyä tarkastetaan sen pettämistapa.
Mitatusta murtokuormasta voidaan laskea laminaatin taivutuslujuus eli normalisoitu taivutusjännitys murtohetkellä. Kolmipistetaivutuksessa tämä saadaan lausekkeesta
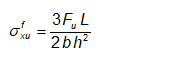
(7.8)
missä Fu on murtokuorma ja b on koesauvan leveys. Nelipistetaivutuksessa vastaava taivutuslujuuden lauseke on
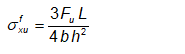
(7.9)
Laminaatin taivutuskimmomoduli saadaan määritettyä kuorma/taipuma-kuvaajan lineaariselta alueelta valitusta voimasta F ja sitä vastaavasta sauvan keskikohdan taipumasta w. Kolmipistetaivutuksessa taivutuskimmomoduli saadaan lausekkeesta

(7.10)
missä korjauskerroin S ottaa huomioon sen, että osa sauvan taipumasta johtuu laminaatin liukumasta eli leikkausmuodonmuutoksesta. Korjauskertoimen määrittelee lauseke
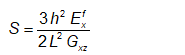
(7.11)
missä Gxz on koesauvan liukumoduli xz-tasossa (kuva 7.10). Nelipistetaivutuksessa taivutuskimmomoduli saadaan vastaavasti lausekkeesta
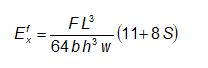
(7.12)
Mikäli materiaaliyhdistelmä käyttäytyy lineaariselastisesti murtoon asti, taivutuslujuudesta ja taivutusmodulista saadaan laskettua myös laminaatin pintojen venymät murtohetkellä. Murtumismuodon tarkistus osoittaa, onko sauva pettänyt ensiksi veto- vai puristuspuolelta. Jälkimmäinen pettämistapa on tavanomaisempi, koska laminaattien puristuslujuus on yleensä vetolujuutta alhaisempi.
Yhdistetyn kuormitustilan takia taivutuskoe ei sovellu laminaatin perusominaisuuksien määritykseen. Normaalisti sillä varmistetaan taivutusjäykkyydelle ja -lujuudelle laskennallisesti saadut arvot. Taivutuskoe on myös hyödyllinen laadunvarmistuksessa, sillä se on yksinkertainen toteuttaa ja antaa indikaation monen materiaali- ja valmistusteknisen parametrin oikeellisuudesta tai virheellisyydestä. Syy taivutuskokeen antamaan poikkeavaan arvoon on useimmiten haettava muilla kokeilla.
Kerrostenvälinen leikkauslujuus (ILSS)
Eräs laminaattirakenteiden heikkouksista on niiden suhteellisen alhainen leikkausjäykkyys ja –lujuus laminaattitasoa vastaan kohtisuorissa tasoissa. Tasoa vastaan kohtisuorassa leikkauksessa laminaatti pettää pääsääntöisesti kerrosten rajapinnasta. Tästä syystä vaikuttavaa kuormitusta kutsutaan usein kerrostenväliseksi leikkaukseksi (InterLaminar Shear, ILS) ja pettämisen aiheuttavaa jännitystasoa kerrostenväliseksi leikkauslujuudeksi (InterLaminar Shear Strength, ILSS).
Laminaattien kerrostenvälistä leikkauslujuutta mitataan eniten ns. lyhyen palkin taivutuskokeella. Paksujen laminaattien ILSS-arvoa mitataan myös edellä kuvatulla Iosipescu-kokeella.
Lyhyen palkin taivutuskokeessa hyvin lyhyttä koesauvaa kuormitetaan kolmipistetaivutuksella (kuva 7.11). Sauvan lyhyydestä johtuen siihen kohdistuva taivutusmomentti jää alhaiseksi ja palkki murtuu pääsääntöisesti leikkautumalla. Koesauvan mitat ja kuormituksen tukiväli riippuvat tutkittavan laminaatin ominaisuuksista. Menetelmä toimii ainoastaan tyydyttävästi, sillä taivutusmomentin ja kuormituspään aiheuttamien paikallisten rasitusten johdosta koekappaleen murtuma ei läheskään aina ole puhdas leikkausmurtuma. Mahdollisia pettämismuotoja on esitetty kuvassa 7.12. Näistä muodot a-c katsotaan hyväksyttäviksi leikkausmurtumiksi.
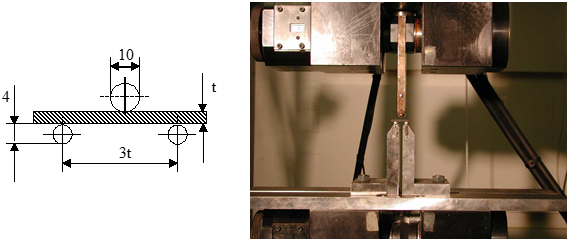
Kuva 7.11 Lyhyen palkin taivutuskoe kerrostenvälisen leikkauslujuuden määrittämiseksi.
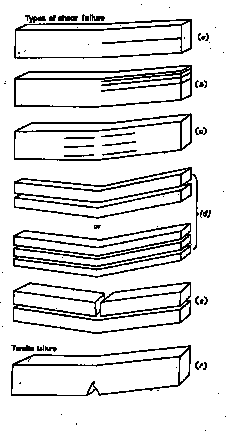
Kuva 7.12 Koesauvan mahdollisia pettämismuotoja lyhyen palkin taivutuskokeessa, muodot a-c hyväksyttäviä kerrostenvälisiä leikkausmurtumia.
7.3.6 Väsyminen
Väsytyskokeissa koesauvat ovat samankaltaisia kuin staattisissa kokeissa. Kokeissa mitataan, montako kuormitussykliä materiaali kestää määritellyllä kuormituksella. Kuormitusnopeus pidetään riittävän alhaisena, ettei koesauva toistuvan kuorman vaikutuksesta lämpenisi. Muovikomposiiteilla lämpeneminen on voimakasta, minkä lisäksi suhteellisen pienet lämpötilamuutokset voivat vaikuttaa merkittävästi väsymisominaisuuksiin. Normaali kuormitusnopeus muovikomposiittien väsytyskokeessa onkin vain muutamia hertsejä. Koe voidaan välillä keskeyttää sauvan vaurioitumisasteen määrittämiseksi. Toisinaan määritetään myös määrätyn väsytysjakson jälkeen koekappaleen staattinen jäännöslujuus.
7.3.7 Viruminen
Laminaattien pitkäaikaisominaisuuksia mitataan tavallisesti virumiskokeilla, tarvittaessa myös relaksaatiokokeilla. Yleensä kokeet ovat veto- tai taivutuskokeita. Koepenkit ovat ympäristökammiossa, johon voidaan säätää haluttu kosteus ja lämpötila. Virumiskokeissa mitataan koekappaleen muodonmuutosta (venymää tai taipumaa) ajan funktiona, relaksaatiokokeessa vastaavasti vakiomuodonmuutostilassa olevaan kappaleeseen kohdistuvaa voimaa ajan funktiona. Kokeiden tulokset esitetään tavallisesti virumis- ja relaksaatiokäyrinä.
7.3.8 Muut ominaisuudet
Loviherkkyys
Tyypillinen lovetun laminaatin lujuuskoe on reiällisen laminaatin vetokoe, jossa käytetään kuvan 7.13 mukaista koekappaletta. Tarvittaessa reiän vaikutus lujuuteen määritetään normaaliolosuhteissa ja laminaatin äärimmäisissä käyttöolosuhteissa eli tilanteissa, joissa laminaatti on hauraimmillaan (kuiva laminaatti, alhainen lämpötila) ja pehmeimmillään (maksimimäärän kosteutta imenyt laminaatti maksimikäyttölämpötilassa).
Staattisten kokeiden ohella reiällisen laminaatin vetokoekappaletta käytetään lovetun laminaatin väsymisominaisuuksien tutkimiseen.
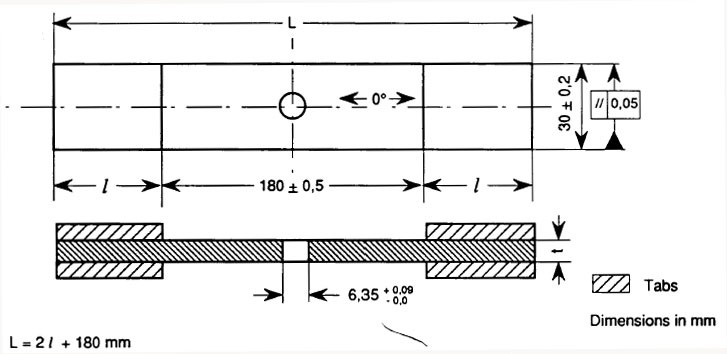
Kuva 7.13 Koesauva reiällisen laminaatin vetolujuuden määritykseen.
Iskunkestävyys
Muovien ja muovikomposiittien iskulujuutta tutkitaan jossain määrin erilaisilla heiluri-iskureilla mittaamalla koesauvan katkaisemiseen tarvittava iskuenergia (kuva 7.14). Kokeet ovat helppoja suorittaa, mutta koetulosten hyödyntämismahdollisuudet käytännön suunnittelutyössä ovat rajalliset. Kokeet sopivatkin lähinnä materiaalivertailuihin.
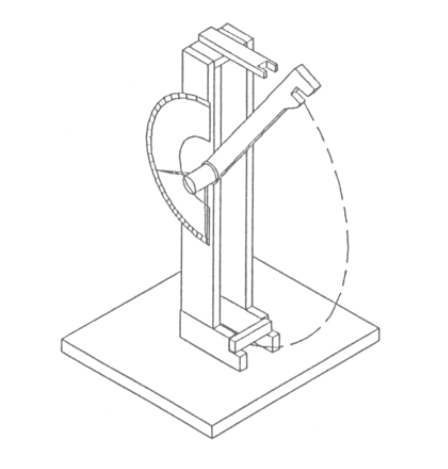
Kuva 7.14 Heiluri-iskurikoe.
Laminaattien iskulujuuden tutkimiseen paremmin soveltuva koe on leveähkön koesauvan tai laminaattilevyn iskukuormittaminen heiluri-iskurilla tai vapaasti putoavalla massalla. Jälkimmäisessä, ns. putoavan massan kokeessa, halutun massan ja muodon omaava iskupää pudotetaan tutkittavan koekappaleen päälle halutulta korkeudelta (kuva 7.15). Iskupään kappaleeseen kohdistamaa voimaa mitataan ajan funktiona iskupään kohdatessa laminaatin ja mahdollisesti lävistäessä sen. Voima/aika-käyrästä voidaan edelleen laskea laminaatin absorboima iskuenergia.
Rakennesuunnittelua hyödyntävää tietoa hankitaan tutkimalla iskun aiheuttaman vaurion suuruutta ja vaurion seurauksia. Kokeissa varioidaan iskupään massaa, muotoa ja nopeutta sekä usein myös koekappaleen kokoa ja tuentatapaa. Parametrit määritetään siten, että iskut vastaavat pahimpia mahdollisia iskuja, joita rakenne voi käytännössä kokea.
Iskujen aiheuttamia vaurioita tutkitaan usein ainetta rikkomattomin tarkastusmenetelmin, sillä vauriot eivät aina näy laminaatin pinnassa. Parhaiten iskuvaurion tarkastukseen soveltuu ultraäänimenetelmä, jolla saadaan määritettyä kohtuullisen hyvin vaurioalueen laajuus. Iskukokeen jälkeen mitataan usein myös vaurioituneen kappaleen jäännöslujuus.
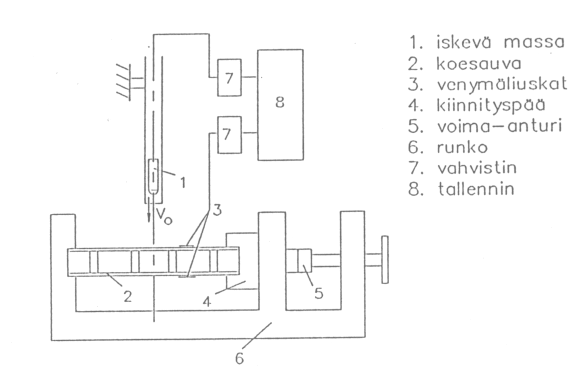
Kuva 7.15 Putoavan massan iskukoe.
Kemiallinen kestävyys
Muovien ja laminaattien kemiallista kestävyyttä tutkitaan kokeellisesti mittaamalla liuokseen upotetun näytteen painonmuutosta. Tarvittaessa kemiallisen kestävyyden määritykseen sisällytetään mekaanisia kokeita, ts. selvitetään myös altistuksen vaikutus laminaatin mekaanisiin ominaisuuksiin.
Palavuus
Materiaalien ja materiaaliyhdistelmien palo-ominaisuuksien mittausmenetelmät voidaan karkeasti jakaa koekappaleen koon mukaan pienen ja suuren mittakaavan kokeisiin. Palovaatimukset ja niihin liittyvät palo-ominaisuuksien määritysmenetelmät ovat osittain tuote- tai sovellusaluekohtaisia.
Pienen mittakaavan kokeissa mitattavia suureita ovat mm. koekappaleen syttyvyys, palonopeus, palamisaika, hehkumisaika ja palavien roiskeiden määrä. Levymäisellä koekappaleella mitattavien suureiden arvo riippuu oleellisesti koekappaleen asennosta. Kokeita tehdäänkin erikseen vaakasuorassa ja pystysuorassa oleville koekappaleille. Kokeiden perusteella materiaalit ja materiaaliyhdistelmät luokitellaan palaviin, itsestään sammuviin ja palamattomiin. Luokitusta voidaan edelleen täsmentää kokeessa mitatun palamisajan perusteella. Yleisesti käytettävän standardin UL94 mukaiset paloluokat ja luokitusperusteet on esitetty taulukossa 7.2. Palaville materiaaleille voidaan myös määrittää pienin happipitoisuus, jossa materiaali ylläpitää paloa.
Palavuuden ohella mitataan palossa syntyvän savun määrää ja koostumusta. Savun määrän mittauksessa mittaustulos riippuu oleellisesti siitä, suhteutetaanko määrä koekappaleen painoon vai tilavuuteen.
Suuren mittakaavan kokeessa koekappale voi olla useita metrejä pitkä ja/tai usean neliömetrin kokoinen. Kokeessa mitataan mm. määritellyllä tavalla palolle altistetun kappaleen syttyvyyttä ja palon etenemisnopeutta.
Taulukko 7.2 Levyjen paloluokitus UL 94:n mukaan. [2]
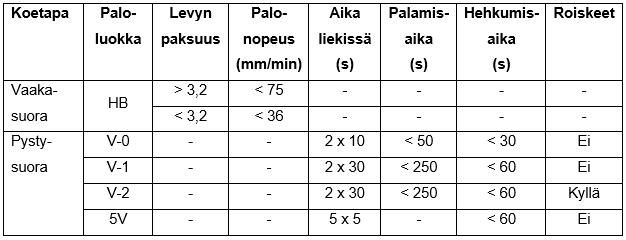
Sähköiset ominaisuudet
Komposiittien sähköisiä ominaisuuksia joudutaan selvittämään erityisesti, kun kehitettävänä on sähkö- ja elektroniikkateollisuuden käyttösovellus. Muidenkin tuotteiden käyttö voi asettaa vaatimuksia esimerkiksi rakenteen sähkönjohtavuudelle. Sähkönjohtavuuden tai -vastuksen ohella tärkeimpiä määritettäviä suureita ovat materiaalin tai rakenteen läpilyöntikestävyys ja dielektriset ominaisuudet. Sähköiset ominaisuudet riippuvat materiaalien ohella oleellisesti ympäristöolosuhteista ja komposiittiin absorboituneesta kosteudesta.
Muovien ja komposiittien sähköisten ominaisuuksien kokeellista määritystä ja koestandardeja on kuvattu mm. lähteessä [2]. Mitattavia vastussuureita ovat tilavuusvastus ja pintavastus. Levymäiselle koekappaleelle vastusarvot voidaan mitata esimerkiksi kuvan 7.16 mukaisella koejärjestelyllä, jossa käytetään kahta pyöreää ja yhtä rengasmaista elektrodia. Läpilyöntikestävyyttä mitattaessa nostetaan tasa- tai vaihtovirran jännitettä, kunnes läpilyönti tapahtuu. Jännitteen nosto voi olla hidas, nopea tai asteittainen.
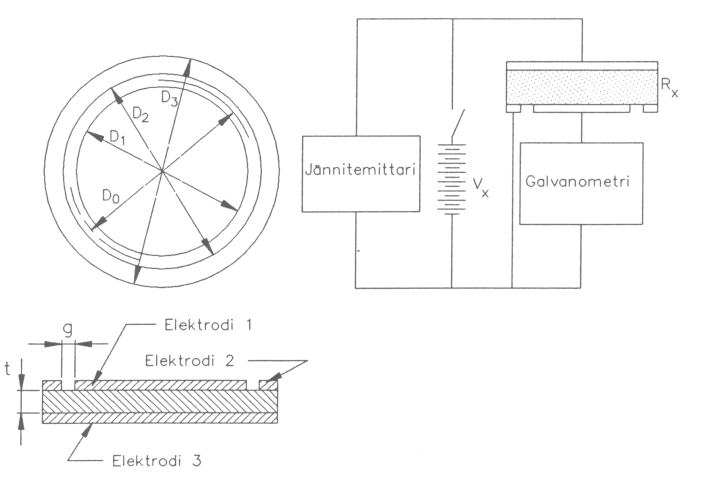
Kuva 7.16 Tilavuus- ja pintavastuksen mittaaminen kahdella pyöreällä ja yhdellä rengasmaisella elektrodilla. [2]
7.3.9 Liitosten ominaisuudet
Mekaanisen liitoksen mitoittaminen edellyttää laminaatin reunapuristuslujuuden tuntemista. Lujuus määritetään kokeellisesti. Kokeisiin soveltuva koesauva ja koejärjestely on esitetty kuvassa 7.17. Mekaanisten liitosten analyysiin liittyvien epävarmuustekijöiden vuoksi kriittisten liitosten lujuus varmistetaan usein myös koko liitoksen lujuuskokeilla.
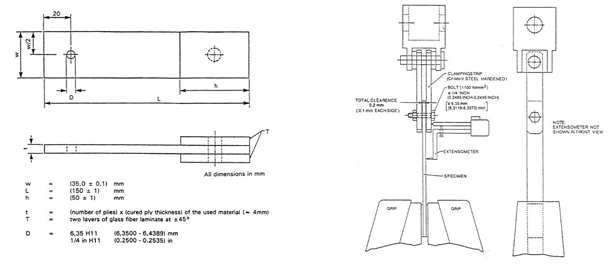
Kuva 7.17 Koesauva ja koejärjestely laminaatin reunapuristuslujuuden mittaamiseen.
Liimojen leikkausjäykkyyttä ja -lujuutta mitataan tavallisesti kahden paksun kappaleen välisen liimasauman leikkauskokeella (kuva 7.18). Koejärjestelyllä minimoidaan saumaan kohdistuvat repivät kuormat. Mitoittamalla liimasauma lyhyeksi, saadaan sauman leikkausjännitys likimain vakioksi (vrt. kuva 6.59). Liimattujen kappaleiden keskinäistä liikettä kuorman funktiona mitataan erityisillä siirtymäantureilla. Voimista ja siirtymistä saadaan edelleen määritettyä liiman leikkausjännityksen ja liukuman välinen vastaavuus.
Toinen standardoitu menetelmä liiman leikkausjäykkyyden ja -lujuuden mittaamiseen on rengasmaisen liimasauman vääntökoe (kuva 7.18). Tässäkin tapauksessa liimasauma on koko alaltaan likimain tasaisesti kuormittunut. Sauman liukuma on verrannollinen mitattavissa olevaan koekappaleiden kiertymään.
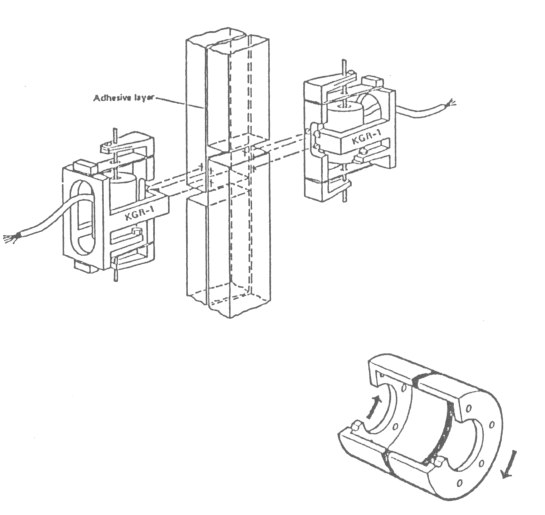
Kuva 7.18 Koemenetelmiä liima-aineen leikkausominaisuuksien määritykseen.
Liiman leikkauslujuutta määritettäessä koekappaleen murtopinta on aina tarkastettava huolellisesti kokeen jälkeen. Tarkoituksena on varmistaa, että mittaustulos kuvaa liiman lujuutta, toisin sanoen että sauman pettämisen syynä on ollut koheesiomurtuma eli liima-aineen pettäminen.
Koska liimasaumoihin kohdistuu useimmiten myös repiviä kuormia, saumojen repimislujuuksien määrittämiseen on kehitetty omat koestusmenetelmänsä. Näistä eniten käytetty on kuvassa 7.19 esitetty sauman repiminen liimattujen kappaleiden taitetuista päistä.
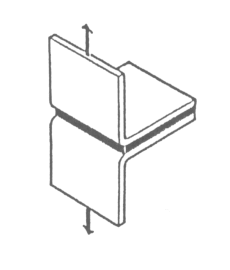
Kuva 7.19 Liimasauman repimiskoe.
Liimasaumojen pitkäaikaiskestävyyttä tutkitaan kuormittamalla limisaumoja halutussa ympäristössä. Saumojen ympäristökestävyyden vertailuun on kehitetty yksinkertainen kiilakoe (kuva 7.20). Siinä kahden levyn välisen liimasauman pää pakotetaan auki ohuella kiilalla, minkä jälkeen koekappale sijoitetaan sääkaappiin haluttuun ympäristöön. Sauman aukeamista seurataan ajan funktiona. Kokeen päätyttyä liimasauma avataan kokonaan ja tarkastetaan sauman vauriotyyppi, jonka tulisi olla koheesiomurtuma. Mikäli vauriotyyppi on osittain tai kokonaan adheesiomurtuma (tartunnan pettäminen), on liimapinnan esikäsittelytapa puutteellinen.
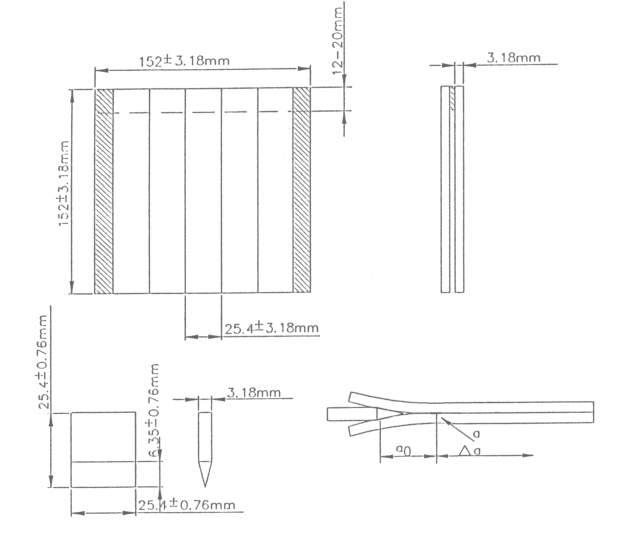
Kuva 7.20 Liimasauman kiilakoe.
7.3.10 Kerroslevyjen ominaisuudet
Kerroslevyissä käytettävien lujitemuovisten pintalevyjen ominaisuudet voidaan määrittää edellisissä kappaleissa kuvatuin menetelmin. Ydinaineen mekaanisista ominaisuuksista tärkeimpiä ovat puristusjäykkyys ja -lujuus paksuussuunnassa sekä leikkausjäykkyydet ja -lujuudet levytasoa vastaan kohtisuorissa päätasoissa.
Ydinaineen puristusominaisuudet määritetään tavallisesti kuormittamalla pyöreää tai nelikulmaista koepalaa kuvan 7.21 mukaisesti. Koska ydinaineen jäykkyys on alhainen, puristuma voidaan usein mitata kuormituspään liikkeestä.
Leikkausjäykkyys ja –lujuus mitataan liimaamalla ydinainepala kahteen paksuun metallilevyyn, jotka edelleen kiinnitetään aineenkoestuskoneeseen (kuva 7.22). Koekappale eli mitattava ydinainepala on niin pitkä, että leikkausjännitysjakautuma voidaan olettaa tasaiseksi koko alueella. Kuormaa F vastaava leikkausjännitys voidaan näin laskea kaavasta
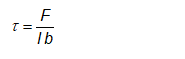
(7.13)
missä l on koekappaleen pituus ja b sen leveys. Liukuma saadaan määritettyä mittaamalla kiinnityslevyjen välistä siirtymää Δ voiman F funktiona. Kun ydinaine käyttäytyy lineaariselastisesti, liukumasta saadaan edelleen määritettyä ydinaineen leikkausjäykkyys kaavalla
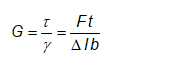
(7.14)
Kerroslevyjä käytetään usein taivutuskuormitetuissa kohteissa, mistä syystä yleisin kerroslevyn koe on taivutuskoe. Kokeet tehdään palkkien kolmi- tai nelipistetaivutuksena samaan tapaan kuin laminaateille (ks. kpl 7.3.5). Koska kerroslevyjen pinnat ovat tyypillisesti ohuita ja ydinaineen jäykkyys alhainen, tuki- ja kuormituspisteiden aiheuttamat paikalliset kuormat ovat kerroslevyjen testauksessa huomattavasti ongelmallisempia kuin laminaatteja testattaessa. Kuormituksia joudutaankin usein jakamaan laajemmalle alueelle, jotta kerroslevy ei pettäisi kuormitus- tai tukipisteen paikallisen kuormituksen vaikutuksesta. Toinen huomionarvoinen seikka kerroslevyn taivutuskokeessa on se, että taipumasta merkittävä osa aiheutuu ytimen liukumasta.
Taivutuskokeiden ohella kerroslevyrakennetta käytetään puristus- ja leikkauskuormitetuissa levyissä estämään levyn lommahtaminen. Kerroslevyn käyttäytymistä puristuskuormituksessa voidaan tutkia esimerkiksi kuvan 7.23 mukaisella koejärjestelyllä. Koetta voidaan kuvan mukaisesti käyttää myös iskuvaurioituneen kerroslevyn puristuskäyttäytymisen tutkimiseen. Koejärjestelyssä on erityisesti huolehdittava siitä, että kuorma johtuu koekappaleeseen tasaisesti. Tämä voidaan koetilanteessa varmistaa koekappaleeseen liimatuilla venymäliuskoilla.
Pintalevyn ja ydinaineen välistä tartuntaa mitataan usein kuvan 7.24 mukaisella kuorimiskokeella. Tämä koe on mahdollista toteuttaa vain, kun kerroslevyn pinta on niin ohut, että se taipuu kuorimisrummun ympärille.
Ydinaineiden ja kerroslevyjen ominaisuuksien määrittämiseen käytetyistä koemenetelmistä on hyvä yhteenveto mm. lähteessä [3].

Kuva 7.21 Ydinaineen puristuskoe.
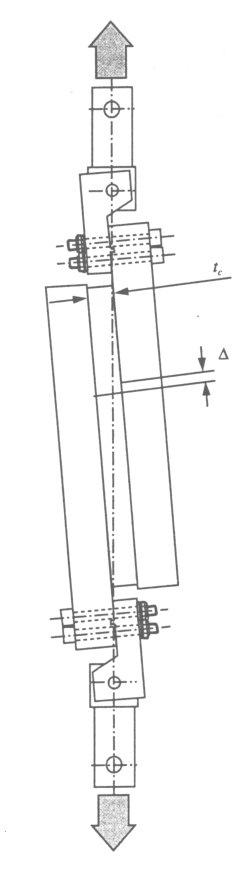
Kuva 7.22 Ydinaineen leikkauskoe.
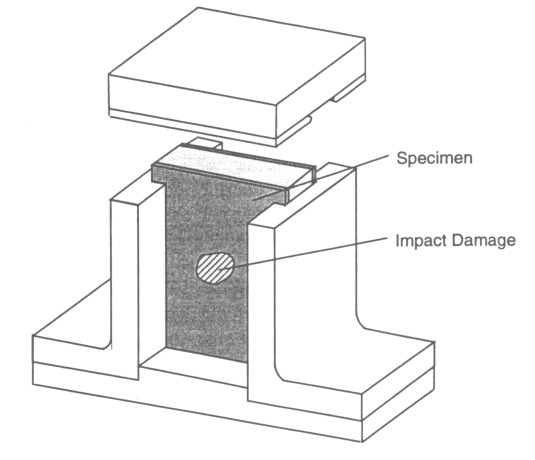
Kuva 7.23 Kerroslevyn puristuskoe.
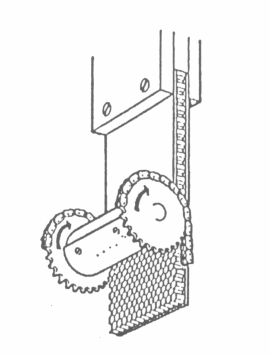
Kuva 7.24 Kerroslevyn pinnan kuorimiskoe.